Exploring the Pros and Cons of Structural Insulated Panels
2 min read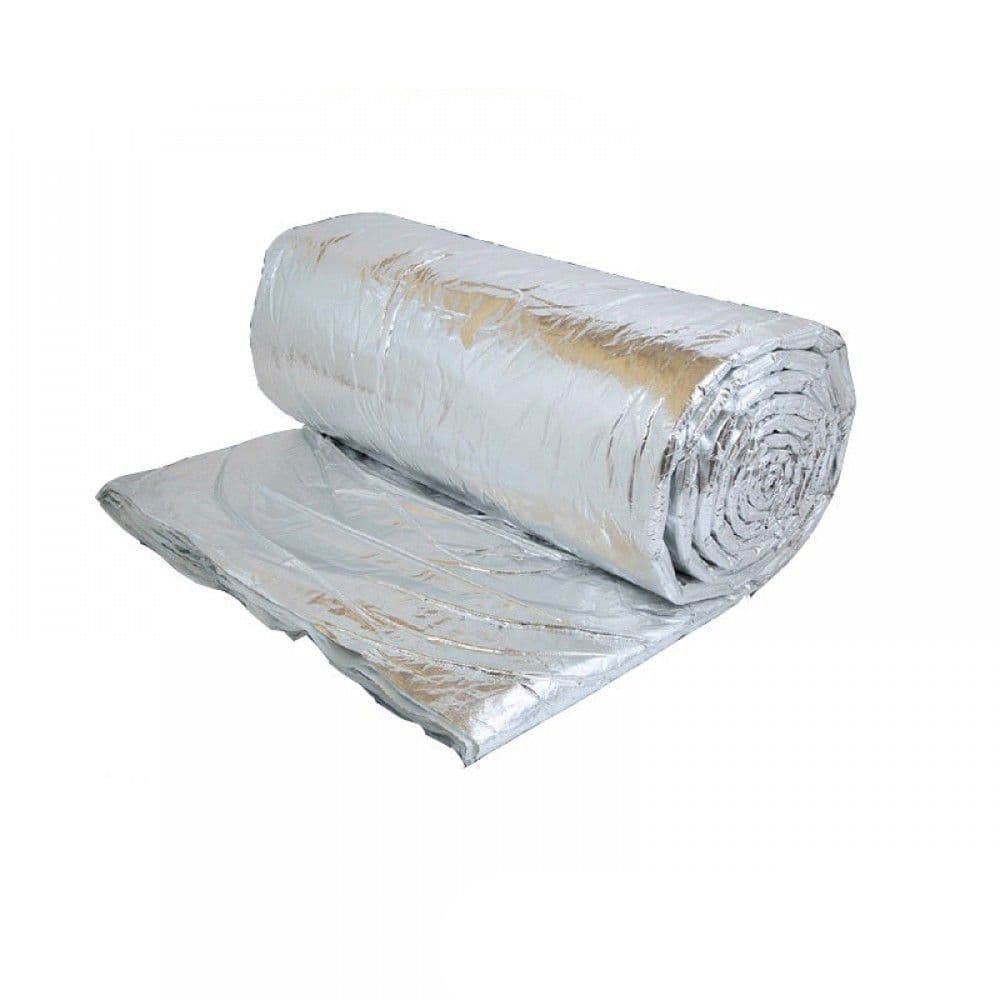
Structural Insulated Panels (SIPs) have gained significant popularity in the construction industry due to their energy efficiency and ease of installation. These panels consist of a foam core sandwiched between two rigid facings, typically made of oriented strand board (OSB). In this article, we will delve into the advantages and disadvantages of using SIPs in construction projects.
Advantages of Structural Insulated Panels:
- Energy Efficiency:
One of the primary advantages of SIPs is their exceptional thermal performance. The foam core provides excellent insulation, reducing heat transfer and minimizing energy consumption. This results in lower heating and cooling costs for homeowners and businesses. - Enhanced Structural Integrity:
SIPs offer superior structural strength compared to traditional construction methods. The combination of the foam core and rigid facings creates a robust and durable panel that can withstand various loads, including wind and seismic forces. This makes SIPs an ideal choice for areas prone to extreme weather conditions. - Quick and Easy Installation:
SIPs are prefabricated off-site, allowing for faster and more efficient construction. The panels can be custom-made to fit specific project requirements, reducing on-site labor and construction time. This accelerated construction process can lead to cost savings and shorter project timelines. - Improved Indoor Air Quality:
The airtight nature of SIPs helps to minimize air infiltration, preventing the entry of pollutants and allergens into the building. This results in improved indoor air quality, creating a healthier and more comfortable living or working environment.
Disadvantages of Structural Insulated Panels:
- Higher Initial Cost:
Compared to traditional construction methods, SIPs may have a higher upfront cost. The specialized manufacturing process and the use of high-quality materials contribute to the increased initial investment. However, it is important to consider the long-term energy savings and potential cost reductions in heating and cooling expenses. - Limited Design Flexibility:
SIPs are prefabricated according to specific design requirements, which may limit the architectural flexibility of a project. Customizations and modifications on-site can be challenging and may require additional expertise and resources. - Moisture Management:
While SIPs are designed to be moisture-resistant, improper installation or maintenance can lead to moisture-related issues such as condensation or mold growth. Proper detailing, vapor barriers, and regular inspections are essential to mitigate these risks. - Transportation and Handling:
Due to their size and weight, transporting and handling SIPs can be more challenging compared to traditional building materials. Specialized equipment and careful planning are necessary to ensure safe delivery and installation.
Conclusion:
Structural Insulated Panels offer numerous advantages in terms of energy efficiency, structural integrity, and installation speed. However, it is crucial to consider the higher initial cost, limited design flexibility, and proper moisture management when opting for SIPs in construction projects. By weighing the pros and cons, builders and homeowners can make informed decisions regarding the suitability of SIPs for their specific needs.