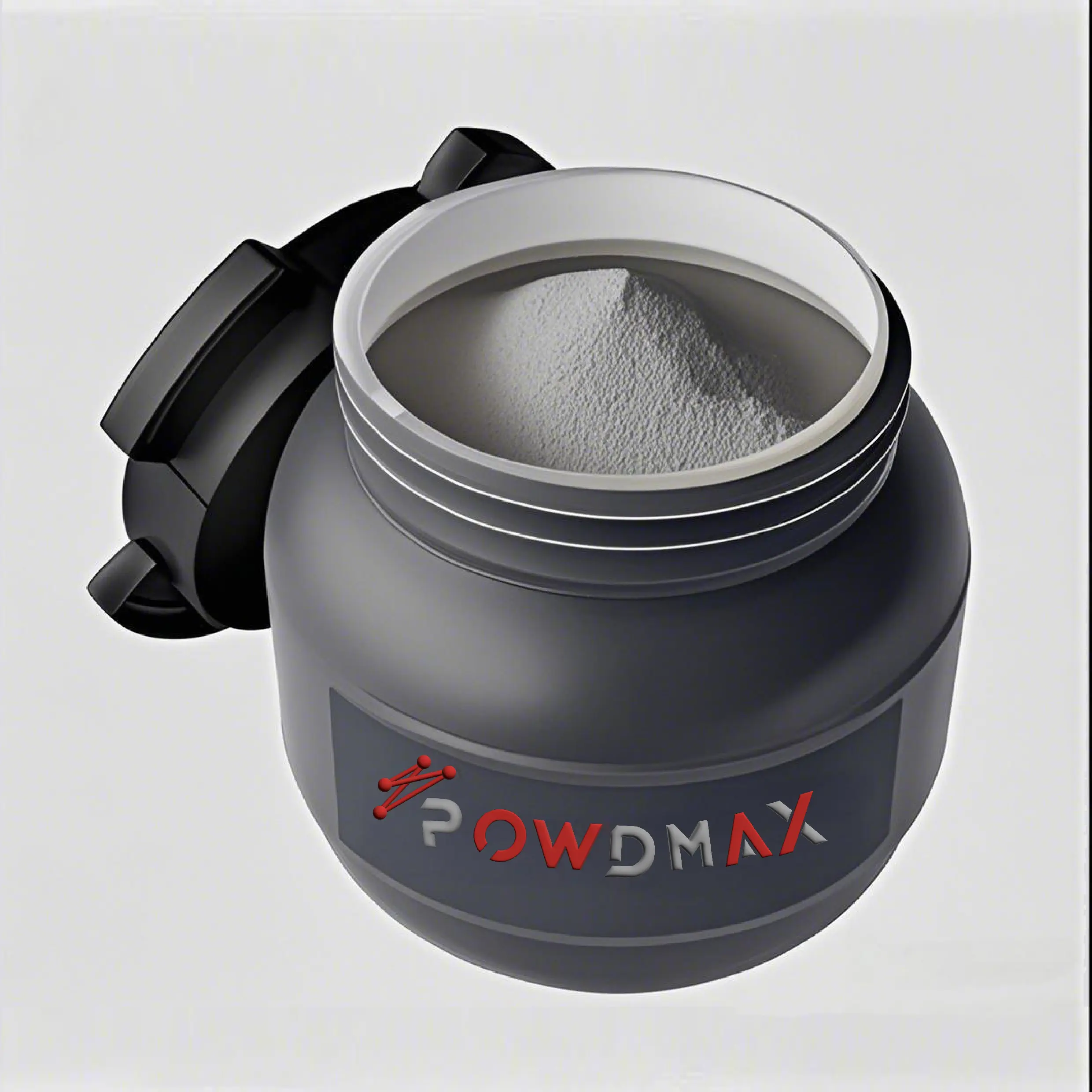
The aerospace industry constantly pushes the limits of performance, durability, and safety. As modern aircraft face increasingly extreme operating environments, the materials used to manufacture their components must deliver superior resistance to heat, wear, and corrosion. This is where Cobalt-Based Powders come in. These advanced powders are essential for optimizing aerospace components, especially in high-stress and high-temperature applications. At Hangrui (Shanghai) Advanced Materials Technology Co., LTD., we specialize in producing high-purity cobalt-based powders that meet the stringent requirements of aerospace manufacturing, especially for additive manufacturing and powder metallurgy applications.
Below, we break down how cobalt-based powders are used to enhance aerospace components—both in performance and production efficiency.
1. Why Cobalt-Based Powders Are Critical in Aerospace
Cobalt-based powders are widely used in the aerospace sector due to their exceptional resistance to heat, oxidation, and wear. These properties are essential for components such as turbine blades, combustors, nozzles, and engine parts that operate under high thermal and mechanical stress. Unlike many other metals, cobalt maintains its strength and structural integrity at elevated temperatures, making it a preferred choice for superalloys used in aircraft engines.
Hangrui’s cobalt powders are produced using advanced atomization techniques that ensure excellent flowability, uniform particle size distribution, and spherical shape—ideal for precision aerospace manufacturing.
2. Enhancing Component Life Cycle with Wear Resistance
One of the most important roles of cobalt-based powders is in increasing the wear resistance of aerospace components. Jet engines, for example, contain parts that move at high speeds and experience constant friction. Cobalt’s natural toughness and ability to form hard phases in alloys help minimize wear, extending the life of critical engine components.
Powders can be applied using thermal spray or laser cladding to form a hard-facing layer, which resists abrasion and fatigue. Hangrui’s cobalt-based alloy powders offer excellent metallurgical bonding, ensuring strong protective surfaces even in demanding environments.
3. Improving Heat Resistance in High-Temperature Zones
Aircraft engines often operate above 1,000°C, where typical alloys start to degrade. Cobalt-based superalloys retain their mechanical properties in these extreme temperatures. By using cobalt-based powders, engineers can manufacture or coat engine parts to maintain performance over long operating cycles.
Hangrui’s powders are optimized for high-temperature stability, making them suitable for hot section components of jet engines, such as turbine blades and combustion chambers.
4. Supporting Additive Manufacturing for Complex Aerospace Parts
Additive manufacturing (AM), especially metal 3D printing, has become a game-changer in aerospace. Cobalt-based powders enable the production of lightweight, complex, and customized components with minimal material waste.
Hangrui offers AM-grade cobalt powders with controlled morphology, high purity, and low oxygen content. These characteristics are essential to achieve high-quality builds with excellent surface finish and mechanical performance. Cobalt-chromium alloys are particularly popular in 3D-printed aerospace components due to their strength and oxidation resistance.
5. Enhancing Corrosion Resistance for Longer Component Life
Aircraft components, especially those exposed to harsh environments such as salt-laden air or aggressive chemicals, must resist corrosion to remain safe and efficient. Cobalt-based powders, especially those containing chromium and molybdenum, form protective oxide layers that prevent surface degradation.
For applications like exhaust parts, afterburner liners, and structural fasteners, cobalt alloys reduce the risk of corrosion-related failures. Hangrui’s powders are designed to deliver consistent corrosion performance, even under fluctuating environmental conditions.
6. Tailoring Material Properties Through Alloy Design
One key advantage of using cobalt-based powders is the ability to tailor alloy compositions to meet specific performance requirements. Whether it’s enhancing creep resistance, improving fatigue life, or balancing toughness and hardness, cobalt-based alloys offer design flexibility.
At Hangrui, we work closely with clients to develop custom cobalt alloy powders that align with precise aerospace engineering needs. This collaborative R&D approach ensures that the final components meet or exceed regulatory and functional expectations.
7. Meeting Stringent Aerospace Quality Standards
Quality and consistency are non-negotiable in aerospace. Hangrui’s production facilities follow strict quality control processes, including particle size analysis, chemical composition checks, and purity validation. Our cobalt-based powders are produced in ISO-certified environments and are traceable throughout the supply chain.
With three large-scale production plants and state-of-the-art testing equipment, Hangrui ensures that every batch of cobalt-based powder meets aerospace-grade specifications.
Conclusion
When it comes to pushing the boundaries of performance in aviation, Cobalt-Based Powders are indispensable. From extending engine life to enabling precision additive manufacturing, cobalt-based materials offer unmatched advantages in aerospace applications. Hangrui (Shanghai) Advanced Materials Technology Co., LTD. provides aerospace manufacturers with high-quality cobalt powders engineered for demanding conditions, ensuring safety, durability, and innovation.
As aerospace technologies evolve, cobalt-based powders will continue to play a key role in shaping the future of flight—one component at a time.
www.powdmax.com
Hangrui (Shanghai) Advanced Materials Technology Co., LTD.