Inside Topfeel’s Makeup Bag Manufacturing Process
4 min read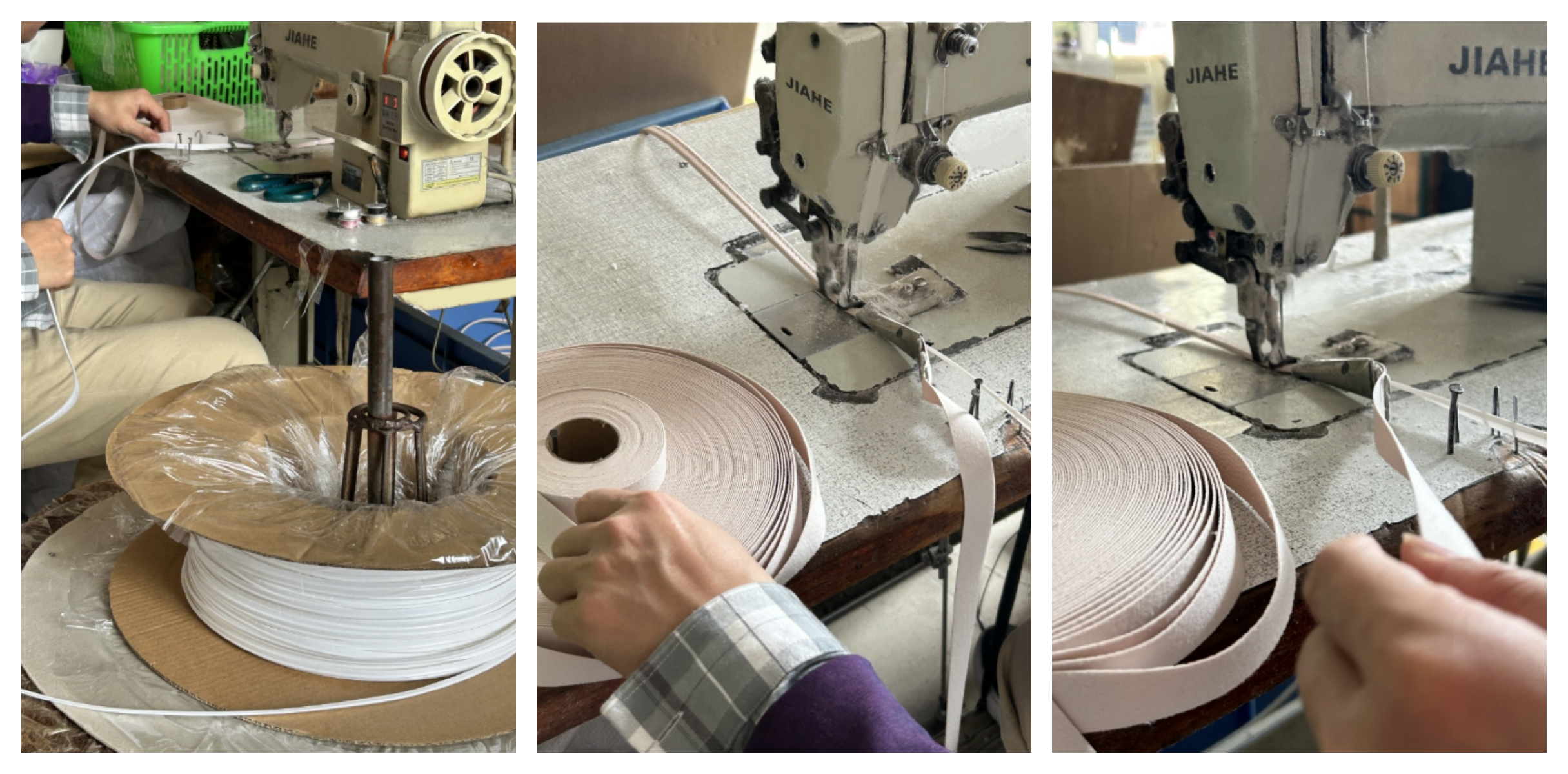
In the OEM/ODM customization cooperation of cosmetic bags, the most frequently asked questions by brand owners, wholesalers, and purchasers of gift channels are:
· Why is MOQ 1,000 pieces?
· Why would changing a structure affect the delivery date?
· What is the normal delivery cycle?
· Does the factory have professional manufacturing capabilities?
These issues may seem independent, but in fact, they are all related to one core: whether there is sufficient understanding of the production process.
For customers who pursue flexible customization, high cost performance and quick delivery, mastering the production process is not only a "knowledge reserve" before procurement, but also the foundation for ensuring the smooth implementation of the project:
1. Understand the rationality of delivery dates: Avoid affecting quality due to blindly compressing time;
3. Enhance customization efficiency: Confirm the feasibility of structure, process and materials in advance to reduce modification costs;
3. Judging the professionalism of suppliers: The process details can reveal whether the factory has mature production lines and the ability to integrate customization.
This article will take you deep into Topfeel's cosmetic bag factory, helping you understand how a custom-made cosmetic bag is manufactured.
The Factory Strength of Topfeel
To understand the production process, it is necessary to start with the basic capabilities of the factory.
Factory Scale and Equipment
· 5,000㎡ standard factory
Be capable of ensuring the smooth progress of large quantities of orders
· 10 mature production lines
Meet the concurrent production of multi-category orders
· 5 cutting machines
It features high precision, can reduce human errors during the cutting process, and enhance material utilization and efficiency.
· 9 computerized sewing machines
By controlling the density of stitches and the thread trajectory through the program, the sewn parts of the bag can be made more firm and exquisite.
Professional Talents
· 2 CAD pattern makers
Through CAD software, pattern making and structural design are carried out. Based on the design drawings or creative ideas provided by the customer, the shape, proportion and internal structure of the bag are precisely restored.
· 5 sample developers
Proficient in various material cutting, sewing and structural optimization techniques, capable of converting drafts into 1:1 restored physical samples.
With systematic equipment configuration and an experienced team, Topfeel ensures that every cosmetic bag meets the quality standards and delivery requirements expected by customers.
Topfeel's Standardized Production Process for Cosmetic Bags
Having solid manufacturing capabilities is only the foundation. To transform an conceived cosmetic bag into a mass-produced product, a complete set of orderly and standardized production processes is also required.
1. Material Procurement
After confirming the style and material, our purchasing staff will uniformly purchase the main materials, auxiliary materials(lining, padding & reinforcement) and accessories.
We insist on establishing long-term cooperative relationships with high-quality material suppliers to ensure the stability of the material supply chain.
Meanwhile, we will conduct incoming quality inspection on each batch of main and auxiliary materials to ensure controllable color differences, stable physical properties, and meet export and brand-level standards.
· Reference for material preparation cycle: 7 to 10 days
Depend on the type of material required. If the material is special, the time may be extended.
2.Customization
Topfeel has professional custom developers who can quickly respond to customers' demands for drawings or samples, and provide customized services such as structural pattern making and color matching. We support a variety of logo and pattern customization processes to meet the diverse expressions of brands.
Want to learn more? Click here to explore our customization techniques.
· Reference cycle for process customization: 10 to 15 days
3. Precision Cutting
After all the materials are gathered, the cutting process will begin.
Topfeel is equipped with high-precision cutting machines, which can reduce human errors during the cutting process and improve cutting efficiency, ensuring that the dimensions of fabric, lining, interlayer and other cut pieces are consistent.
4. Sewing Process
The sewing process is the core stage of shaping a cosmetic bag, involving multiple sub-steps. Topfeel ensures the beauty and firmness of every stitch and thread through a standard procedure:
· Sew bone strip
Sew bone strips (generally waterproof materials such as PVC/TPU) into strip-shaped leather materials.
· Zipper sewing
Sew the zipper patch and the main zipper to ensure the zipper does not get stuck or derail easily during daily use.
· Handle strap sewing
Step 1:Automatic sewing of hand strap
Through high-speed automatic sewing equipment, hand-held straps are sewn in batches to ensure uniform threading and consistent tension.
In actual production, a skilled worker can continuously sew a lifting belt that is restricted by 30 meters.
Step 2:Sew the handle strap to the bag pieces
The sewn strap is precisely combined with the bag body through a computerized sewing machine. This step ensures that the bag does not easily come loose or break under load.
· Sewing two different pieces together
The bag flap, bottom panel, and inner lining are sewn together. Faux stitching is sometimes used to enhance seam appearance, serving both decorative and functional purposes.
· Reinforce edge with bone strip
Sew the sewn bone strips along the edge of the makeup bag lid or bottom to enhance the three-dimensional effect and support of the bag.
· Overedging seam & sew the straps from the inside
Fabrics or leather are prone to fuzz after cutting. By wrapping the edges of the material to seal them, the situation of material shedding can be avoided.
Meanwhile, sewing the straps from the inside can hide the sti
www.topfeelbag.com
Topfeel