Decoding Weak Links: Analyzing the Vulnerabilities in Welding Joints
3 min read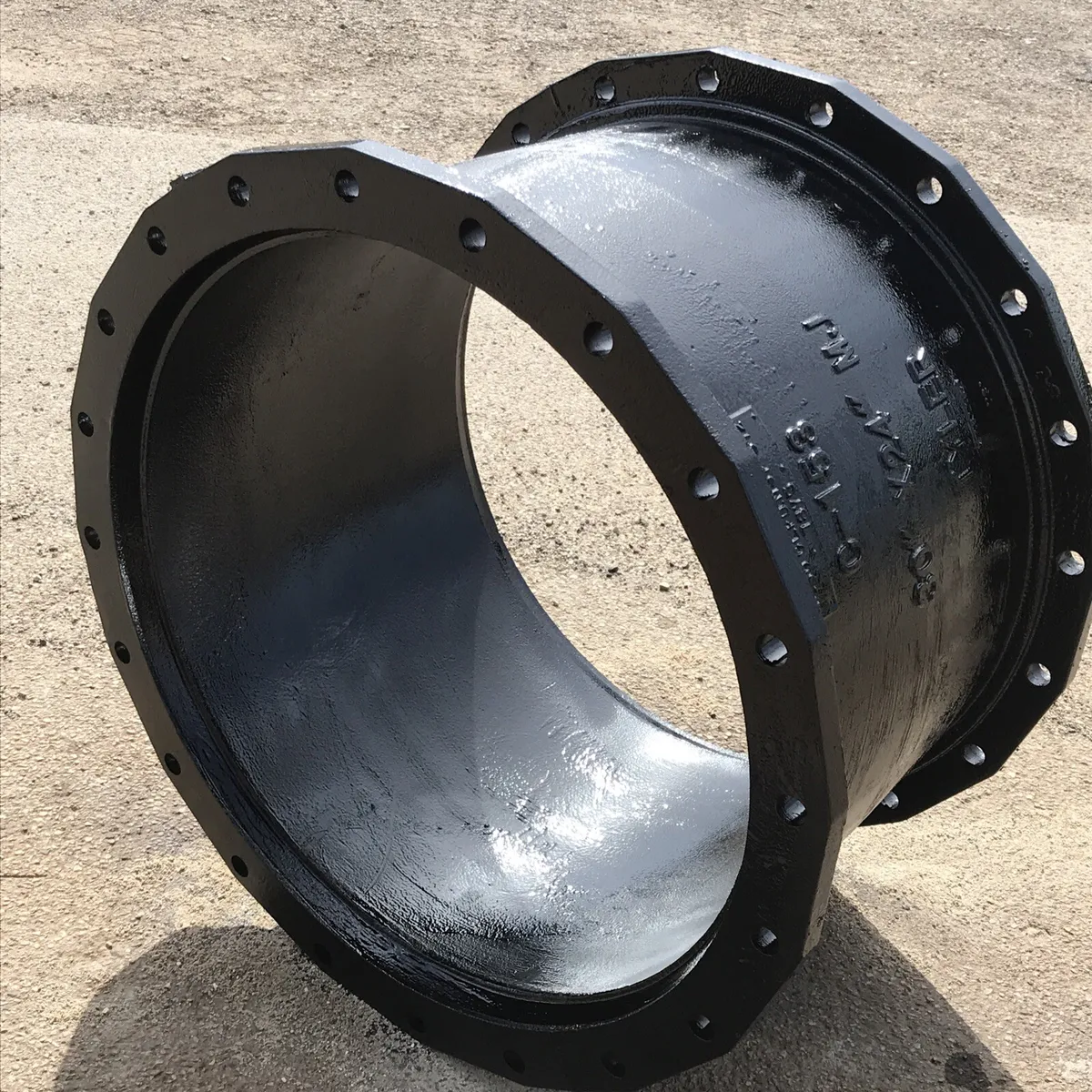
In the intricate world of welding, the strength and reliability of joints are paramount considerations. Engineers and fabricators often find themselves questioning which welding joint is the weakest, seeking to understand the factors that contribute to vulnerabilities in welded connections. This comprehensive exploration aims to unravel the complexities surrounding weak links in welding joints, examining different joint types, influencing factors, and strategies for strengthening these crucial components.
I. Types of Welding Joints: Diverse Configurations
1. Butt Joints:
Butt joints involve the alignment of two workpieces edge-to-edge. While they are commonly used, the strength of butt joints can be influenced by factors such as weld penetration and alignment precision.
2. Lap Joints:
Lap joints involve overlapping two workpieces. The strength of lap joints is susceptible to factors like the degree of overlap, weld quality, and the materials being joined.
3. Fillet Joints:
Fillet joints are formed at the intersection of two workpieces, creating a triangular cross-section. The strength of fillet joints is influenced by factors such as leg length, throat depth, and the welding process used.
II. Factors Influencing Weakness in Welding Joints: Unraveling the Culprits
1. Lack of Fusion:
Insufficient fusion between the weld metal and the base material can result in weak joints. This issue may arise from inadequate heat input, improper welding technique, or improper preparation of the joint surfaces.
2. Inadequate Penetration:
Inadequate penetration occurs when the weld metal does not fully penetrate the joint. This can weaken the joint's structural integrity, especially in applications subjected to high loads or stresses.
3. Misalignment:
Misalignment during the welding process can lead to uneven stress distribution, creating weak points in the joint. Proper alignment is crucial for ensuring uniform strength across the welded connection.
III. Common Weaknesses in Specific Joint Types: Pinpointing Vulnerabilities
1. Butt Joint Weaknesses:
Butt joints may be susceptible to lack of fusion along the root, inadequate penetration, or incomplete joint preparation. The vulnerability depends on factors such as joint configuration, material thickness, and welding parameters.
2. Lap Joint Weaknesses:
Lap joints are prone to weaknesses at the overlap region. Issues like incomplete fusion or inadequate overlap can compromise the joint's strength, especially in applications where shear forces are prevalent.
3. Fillet Joint Weaknesses:
Fillet joints may exhibit weaknesses at the toe or root if welding parameters are not optimized. Issues like underfilled welds or excess convexity can contribute to vulnerability in fillet joints.
IV. Strengthening Strategies: Enhancing Welded Joint Performance
1. Improved Welding Techniques:
Optimizing welding techniques, such as adjusting heat input, travel speed, and electrode angle, can enhance fusion and penetration, addressing common weaknesses in welded joints.
2. Pre-weld Joint Preparation:
Thorough joint preparation, including cleaning, beveling, and proper fit-up, is essential for preventing issues related to lack of fusion, incomplete penetration, and misalignment.
3. Quality Assurance Measures:
Implementing rigorous quality assurance measures, including non-destructive testing methods like ultrasonic testing or radiography, can help identify potential weaknesses in welded joints before they become critical.
V. Emerging Technologies and Innovations: Charting the Future of Welded Joints
1. Advanced Welding Processes:
Technological advancements in welding processes, such as laser welding or friction stir welding, offer opportunities to improve joint strength and overcome traditional weaknesses associated with conventional welding methods.
2. Predictive Modeling and Simulation:
The use of predictive modeling and simulation tools allows engineers to anticipate potential weaknesses in welded joints and optimize welding parameters for improved performance.
VI. Conclusion: Navigating the Path to Stronger Welded Connections
In conclusion, understanding which welding joint is the weakest involves a nuanced analysis of joint types, influencing factors, and strategies for improvement. Engineers and fabricators must navigate the complexities of welding processes, address vulnerabilities, and embrace emerging technologies to ensure the creation of robust and reliable welded connections. This exploration serves as a guide for those seeking to strengthen the links in the intricate chain of welding technology, forging a path towards stronger and more resilient joints.