Precision in Every Turn: Unveiling the Advantages of Threaded Joints in Engineering
2 min read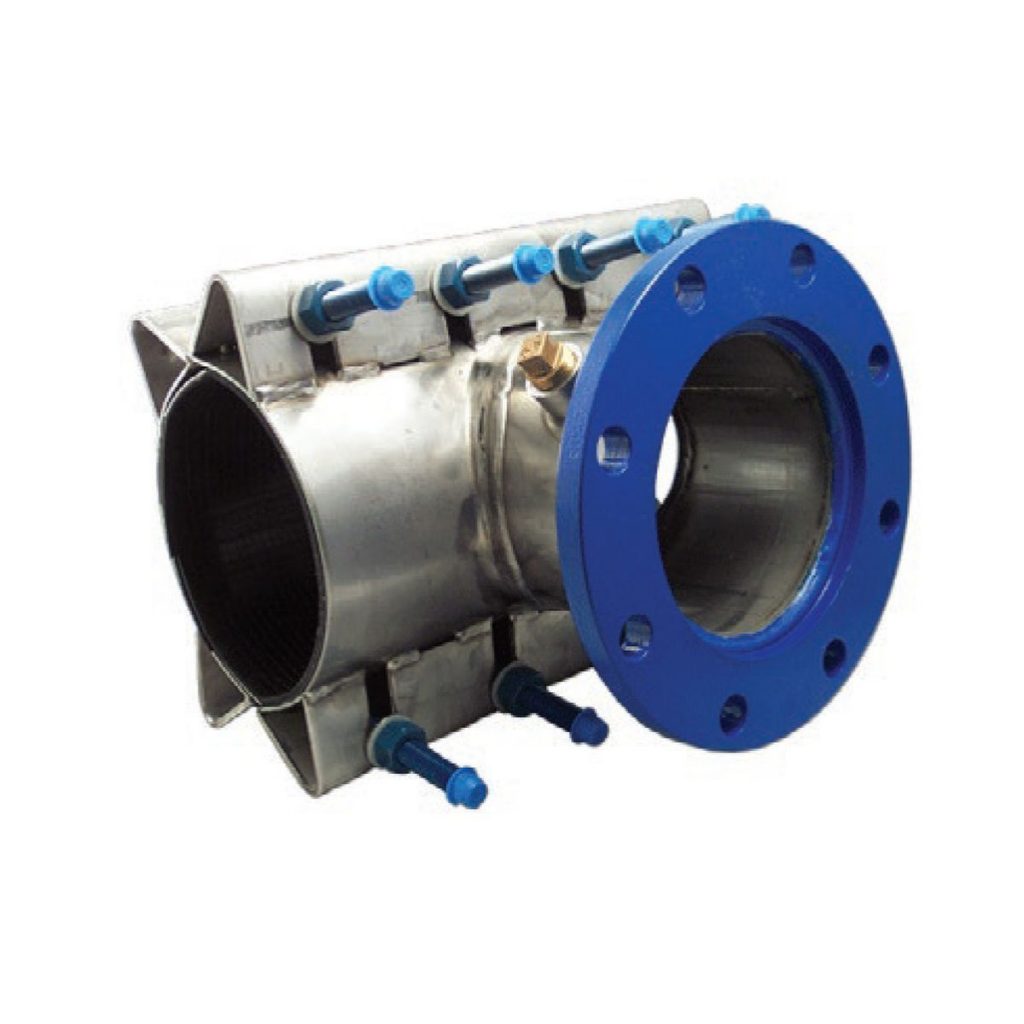
In the intricate world of engineering, the choice of jointing methods plays a pivotal role in determining the efficiency, reliability, and longevity of structures. One such method that stands the test of time is threaded joints. This article explores the advantages threaded joints bring to the table, unraveling the precision, versatility, and practical applications that make them a cornerstone in various industries.
I. Fundamental Characteristics of Threaded Joints:
A. Definition and Mechanism:
1. Threads as Helical Projections
2. Role in Forming a Secure Connection
B. Common Thread Types:
1. Unified National Coarse (UNC) Threads
2. Unified National Fine (UNF) Threads
3. Metric Threads
II. Advantages of Threaded Joints:
A. Ease of Assembly and Disassembly:
1. Simplified Installation Processes
2. Facilitates Maintenance and Repairs
B. Cost-Effectiveness:
1. Reduced Labor Costs in Assembly
2. Minimized Need for Specialized Equipment
C. Versatility in Applications:
1. Adaptability to Various Materials
2. Suitable for a Range of Industries
III. Load-Carrying Capacity:
A. Uniform Distribution of Loads:
1. Mitigating Stress Concentrations
2. Enhanced Strength in Load-Bearing Applications
B. Thread Engagement:
1. Calculating Effective Thread Engagement
2. Ensuring Optimal Load Transfer
IV. Resistance to Vibrations and Shock:
A. Self-Locking Mechanism:
1. Prevention of Spontaneous Loosening
2. Ideal for Dynamic and Vibratory Environments
B. Damping Effects:
1. Absorption of Vibrations
2. Enhanced Stability in Moving Parts
V. Sealing and Leak Prevention:
A. Tapered Thread Design:
1. Improved Sealing Performance
2. Applications in Fluid Systems and Pipelines
B. Thread Sealants and Lubricants:
1. Enhancing Thread Integrity
2. Reducing the Risk of Corrosion
VI. Time-Efficient Installation:
A. Rapid Assembly Processes:
1. Ideal for Mass Production
2. Reduced Downtime in Construction
B. On-Site Adjustability:
1. Flexibility in Field Installations
2. Tailoring Connections to Specific Requirements
VII. Threaded Joints in Specific Industries:
A. Automotive Engineering:
1. Threaded Fasteners in Vehicle Assembly
2. Applications in Chassis and Engine Components
B. Aerospace and Aviation:
1. Precision Threaded Joints in Aircraft Construction
2. Weight Reduction and Structural Integrity
C. Plumbing and Pipelines:
1. Threaded Connections in Water and Gas Systems
2. Resistance to Leakage in Plumbing Applications
VIII. Considerations for Optimal Performance:
A. Proper Thread Design and Specifications:
1. Matching Threads to Application Requirements
2. Compliance with Industry Standards
B. Regular Inspection and Maintenance:
1. Detecting Thread Wear and Corrosion
2. Proactive Measures for Long-Term Reliability
Conclusion:
As we thread our way through the intricacies of engineering connections, the advantages of threaded joints become evident. This article serves as a comprehensive guide, shedding light on the precision, versatility, and efficiency threaded joints bring to diverse industries, cementing their position as a reliable and indispensable jointing method.